World-Class Tooling Capabilities Worldwide
Building upon a rich history of tooling innovations, today MGS continues to build high-precision, high-volume tools with high-cavitation and extremely tight tolerances – with extraordinary speed-to-market. Our global tooling experts design, build and manage hundreds of multi-cavity precision injection molds per year, partnering across global teams to help innovators ensure reliable, repeatable success. With extensive design for manufacturability (DFM) and simulation capabilities, modular pilot Fast-Track Tooling for early product launches, additive manufacturing capabilities and laser texturing experience, our focus in on delivering the highest-performing high-volume, high-quality healthcare molds to our customers.
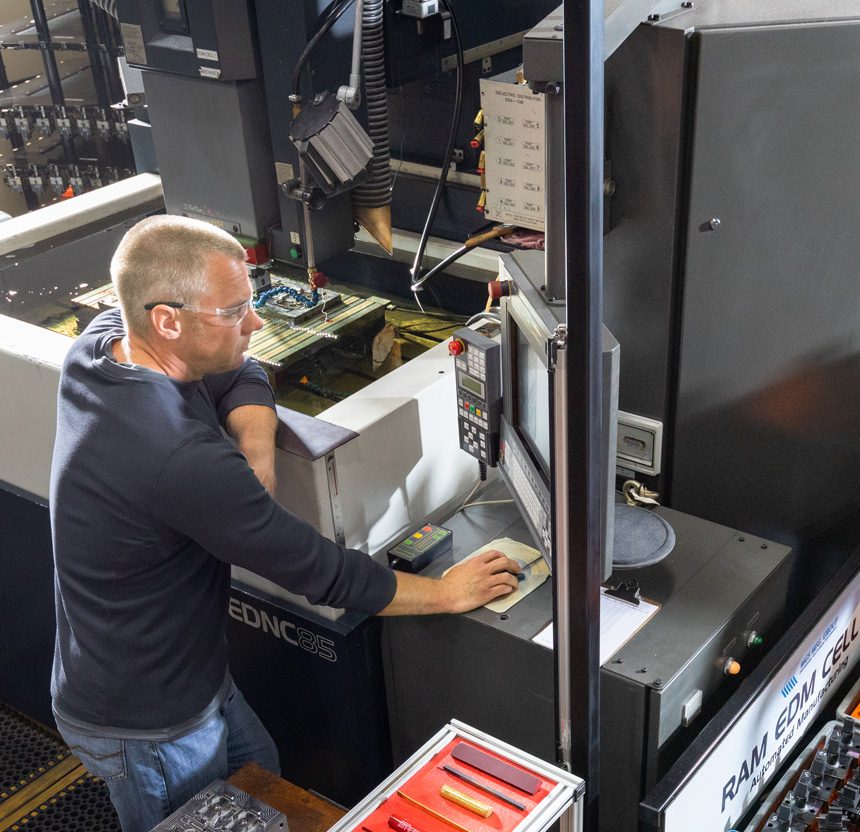
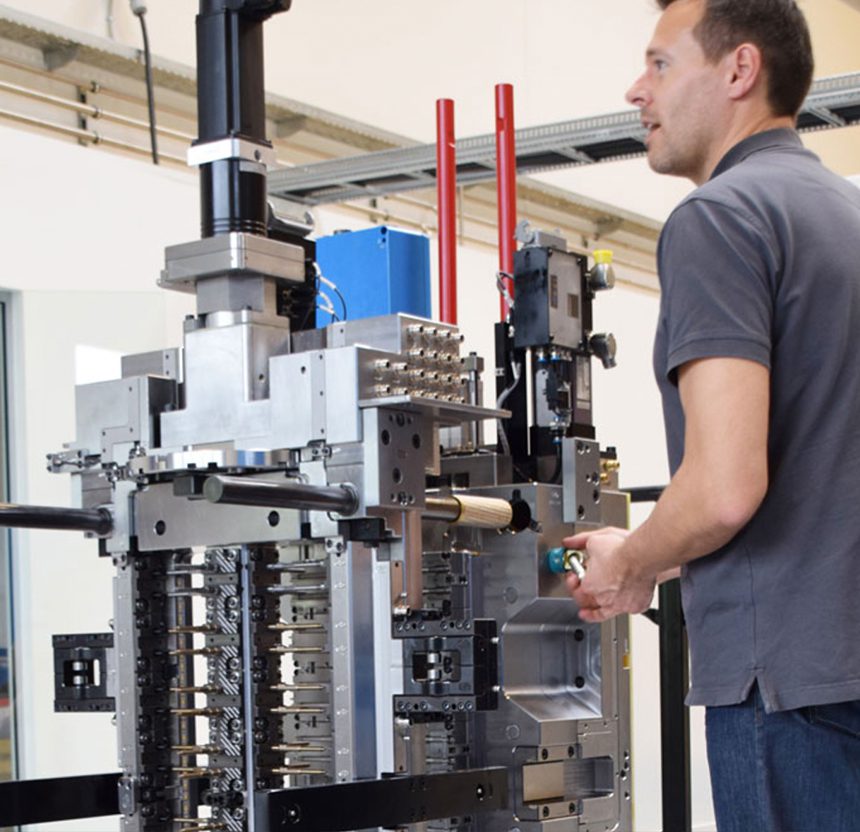
Unmatched levels of craftsmanship, tenacity and drive give leading Pharma, Diagnostic and MedTech companies the confidence that we’ll get it done right – the first time.
Whether introducing new tools for your product launch or transferring tools to any one of our global manufacturing facilities, our state-of-the-art tooling centers and in-house tool repair shops ensure the ongoing performance of your tooling.
Our experts can handle your toughest applications, we can hold repeatability of tolerances daily at +/- .0005, and when the project and budget can support it, our shop can hold +/- .0001.
Better Mold Technologies for Better Results
Multi-Component
Features multiple materials within the same production cell to consolidate parts. Can introduce inserts through robotic placement during molding processes. Results in reduction of downstream assembly and multiple manufacturing cells.
High-Speed & Cavitation
MGS can produce molds up to 288 cavities for high-volume production. These molds can operate with sub three-second cycles to accelerate production while maintaining quality.
Stack Molds
Molds for high-volume production that can produce two-to-four times the volume of single-face molds. Feature multiple parting lines and faces to maximize the use of single machine tonnage.
Auto Unscrewing
Allows for the production of molded-in threads. System actuation offerings are Servo, hydraulic or mechanical.
Achieving Moldmaking Excellence Globally
Adding Value with Extensive Tooling Expertise
Customers have access to a vast scope of knowledge and expertise from our experienced toolmakers. The outcome? High-precision, long-lasting molds that meet your ongoing project needs. Additional resources include:
- Conformal Cooling
- Selective Metal Laser Sintering (SLS)
- 5-Axis Laser Texturing
- Servo-Driven Mold Movements
- Predictive and Preventative Maintenance
Industry-Leading Facilities
Upfront Tooling Support to Accelerate Timelines
Early Supplier Involvement & Design for Manufacturability
We offer expert support in early supplier involvement (ESI) and design for manufacturability (DFM) to evaluate part designs while ensuring the best possible outcomes for your process. Our medical product engineering experts leverage decades of experience combined with best-in-class software to provide an in-depth analysis and report of your program to equip you with the information you need to succeed.
Fast-Track Tooling Expertise
Together with our customers, we design solutions that are better, faster and cost-effective. Our Fast-Track tooling concept utilizes standard and modular components, customizable with your program’s unique needs, to evaluate your program before investing in full-scale production tooling.
Test and Validation
MGS customers have access to state-of-the-art test and innovation centers around the world to ensure their programs are ready for regulatory approval in both the United States and Europe. We gather the critical information you need to support you from initial review to final file submission.
Contact Us
Talk with one of our global tooling experts today to learn how we can accelerate your time-to-market while exceeding quality expectations.
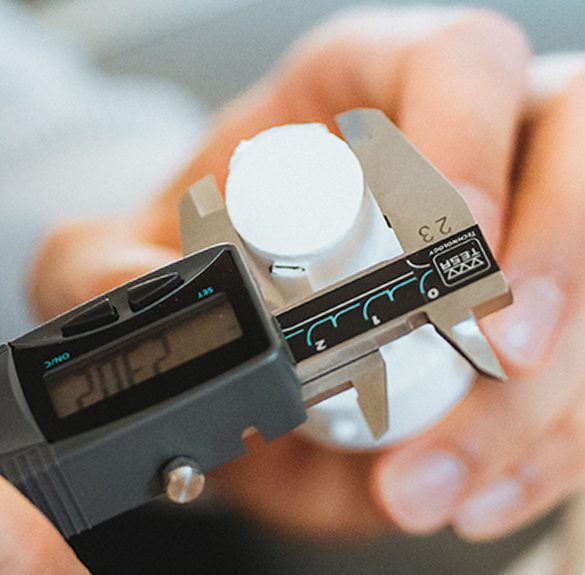